Hull and Deckhouse Construction
Our yachts are hand crafted by one of the oldest and most prestigious marine yards in the Orient. Activa Marine builds our vessels to our own very exacting specifications. In addition, our construction is guided by the requirements of ABS (USA), USCG (USA), NK (Japan), CR (Taiwan), and Lloyds (UK). Furthermore, our pilothouses have been fully inspected and certified by the NMMA as ABYC compliant. This certification is quite significant for a vessel in this size range.
One of the core elements of our construction process is the use of only three main molds; hull, deckhouse, and flybridge. While the tooling is very expensive this approach yields far fewer seams in the finished product and a much more integrated and cohesive vessel. It is far less likely that a vessel so constructed would develop leaks or problems.
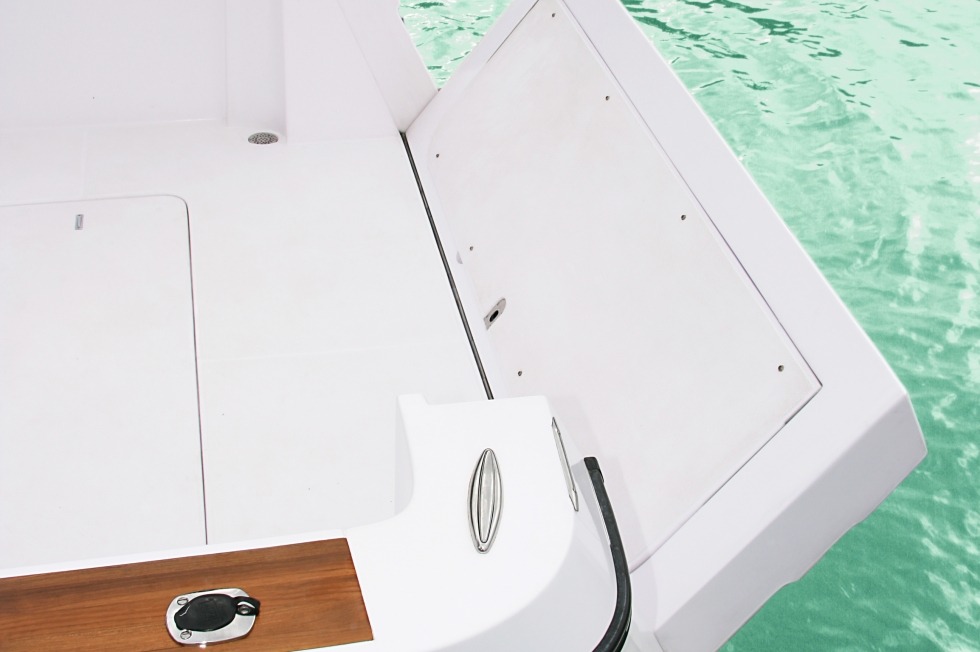
- Our hull is hand applied, biaxially laid, solid FRP below the waterline.
- Vinylester resin is used for hull lay-up in strictly controlled atmospheric conditions.
- High quality Knytex is used as the standard roving however Kevlar is available, as an option, for use in collision zones.
- Our upper hull, deck, deckhouse, and flybridge are cored with high strength, closed cell Divinycell foam and then vacuum bagged. This results in significantly greater strength to weight ratio and eliminates the chance for water incursion and subsequent delamination.
- Our hull to deck joint is through-bolted every 5” (sealed with high strength waterproof sealant) and encapsulated with multiple layers of FRP.
- Our hulls feature a super stiff stringer system which incorporates longitudinal and transverse members as well integration with robust accommodation bulkheads. The resulting monocoque structure is not only tremendously strong but also very quiet under way.
- Structural engine mounting incorporates massive lineal stringers cored with steel beams, cored with Divinycell, and encapsulated with heavy FRP. Custom 316 engine mounts join the engines to the resulting rock solid foundation. As a result noise and engine vibrations are kept to a minimum.
- All areas under leveraged stress, such as stabilization points, running gear attachment points, and railings are reinforced with appropriate backing plates encapsulated in FRP.
- All frameless window systems allow interesting architectural shapes that harmonize with the sculpted fiberglass surfaces. A high-performance urethane adhesive/sealant joins the tempered safety glass to the aluminum-reinforced superstructure.
- All interior surfaces (including storage areas), as well as exterior, are heavily gel coated for both aesthetic and maintenance purposes.